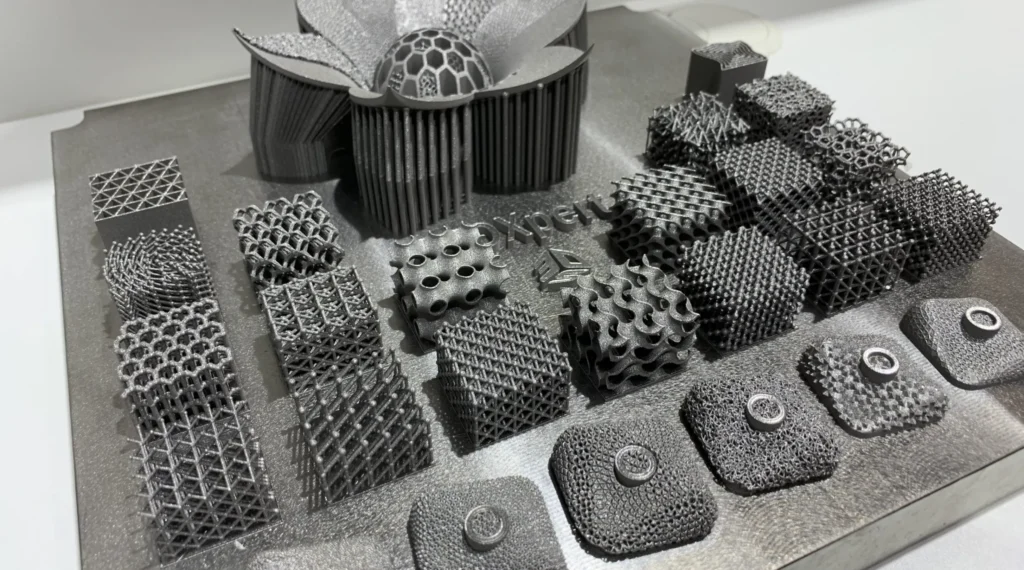
Metal Lattice
Metal lattice structures made by 3D printing are lightweight and strong, making them very efficient industrial components. These structures use patterns of connecting nodes and beams to form complex internal designs that would be difficult or impossible to fabricate using older methods. Because they reduce weight but maintain strength, they are very useful in industries such as aerospace, medical, automotive, and energy.
In this article, we’ll take a look at metal mesh 3D printing technology, including its benefits, issues, applications in industry, and important things to consider when designing.

Benefits of Metal Lattice 3D Printing
Use Less Material and Save Money
3D printing allows people to create mesh structures that use less material but remain strong. Older manufacturing methods require more material to achieve the same strength and therefore cost more. In fields such as aerospace and automotive, using less material means less weight and lower manufacturing costs.
Lightweight Part
Mesh structures make metal parts lighter, making them ideal for industries with high weight requirements. For example, in aerospace, lighter parts help reduce fuel consumption, and in the medical field, lighter implants fit the patient better.
Better Performance
Relative to weight, metal lattices are stronger, handle energy better, and are hard but still light. As a result, they work well for items that need good performance, such as impact-absorbing helmets, impact-resistant components, and medical implants that need to be both flexible and strong.
Better Heat Control
Lattice structures have a larger surface area than solid parts and therefore carry away heat better. This is important for things like heat exchangers, cooling systems for electronic devices and aerospace parts that require good thermal control.
Complex Shapes and Customized Designs
Old machine methods don’t work well for producing detailed lattice designs. But with 3D printing, engineers are able to create the right lattice structure as needed. This means they can make specialty parts for specific industrial needs.
Problems with Metal Lattice 3D Printing
Difficult to Calculate
Making metal lattice designs requires advanced computer tools to check the stresses and weights and determine whether they can be fabricated. Complex lattice pattern files are large, often over 500MB, so powerful computers are required.
Time and Money Required to Print
Although 3D printing wastes less material, complex lattice designs take longer to print because of all the layers of detail that have to be printed. As a result, it can cost more than a physical design, especially when making a large number of items.
Post-Printing Work and Removal of Powders
Metal 3D printing methods, such as direct metal laser sintering and electron beam fusion, require post-printing work, such as removing supports, heat treatment, and surface polishing. In addition, it is difficult to remove residual powder from the detailed lattice structure, so the design needs to consider how to remove the powder.
Strength and Testing
Although lattice structures are very strong relative to their weight, they will behave differently under different forces and stresses. They require extensive testing and computer checks to ensure they are strong enough, especially in critical applications such as aerospace and medical implants.
Industrial Applications of Metal Lattice 3D Printing
Aerospace and Defense
Aerospace companies use metal mesh structures to manufacture lightweight, robust components such as brackets, fuel nozzles, and structural reinforcements. These parts help save fuel, reduce pollution, and make aircraft work better. In addition, defense uses include lightweight armor and impact-resistant materials.
Medical Implants and Prosthetics
People use 3D printed metal lattice structures to make orthopedic implants, spinal cages, and dental prosthetics. The lattice design helps the bone grow into the implant, so the medical device stays in the implant better and lasts longer. People often use titanium for these things because it works well with the human body.
Automotive Engineering
People use lattice structures in electric vehicle (EV) battery boxes, lightweight car parts, and support structures. These designs help reduce the weight of cars and make them work better. In addition, Formula 1 and high-performance car manufacturers use 3D printed metal lattices to make cars lighter and move better through the air.
Heat Exchangers and Thermal Management
Where heat dissipation is needed, use lattice structures in heat exchangers, radiators and cooling components. The larger surface area helps move heat better, which makes power plants, electronic equipment cooling and aircraft thermal control work better.
Industrial Tools and Molds
Metal lattice structures make injection molds, die casting molds and manufacturing supports better. The lattice design allows the cooling channels to work better, so that when many parts are made, the time it takes to make the part is shortened and the life of the mold is extended.
Energy and Power Generation
People use lattice structures in gas turbines, nuclear reactors and hydrogen fuel cells. Lattice structures help air flow better, carry away heat better, and make the structure stronger, thus reducing the energy consumption of the power system.
Types of Metal Lattice Structures
TPMS (Triple Periodic Minimum Surface) Lattice
TPMS lattices, like gyroscopic and diamond structures, are strong but lightweight. These structures are very suitable for medical implants and heat exchangers because the stresses are uniformly distributed in them and they have a large surface area.
Strut-Based Lattices
Lattices are made up of connected beams that form cubic or tetrahedral units. They are frequently used in aerospace and automotive applications to create lightweight and impact-resistant designs.
Planar Lattices
Planar lattices are simple repeating structures, like honeycomb designs. People use them to make lightweight panels and supports.
Design Considerations for Metal Lattice 3D Printing
Lattice Density and Cell Size
Changing the density and size of the lattice cells changes their strength and weight as well as their workability. If you make the lattice denser, it will be stronger, but it will also require more material.
Print Orientation
How the part is oriented during printing affects its strength and the work that needs to be done after printing.
Support Structures
Printing certain lattice structures requires support structures. You must carefully design these support structures to allow for easy disassembly.
Powder Pickup Channels
You need to create channels in the lattice to remove excess powder. This helps the final product to be clean.
Surface Finishing
After printing, you can make the part better by polishing and heating it. This makes the part stronger and better looking.
The Future of Metal Mesh 3D Printing
New software and printing equipment are making a greater variety of metal mesh designs possible. Computers with artificial intelligence can now help engineers create better lattice structures faster. In addition, new methods of printing with different metals at the same time will make lattice parts even better. This means you can make parts that have different properties in different areas.
Metal 3D printing technology is constantly advancing. Because of this, lattice structures will help make industrial parts work better, use less energy, and last longer.
Conclusion
Metal lattice 3D printing technology is making a huge difference in the way we manufacture factories. It allows us to make parts that are lightweight, strong and work well. There are still some issues such as complex computer work and finishing of parts after printing. But the good outweighs the problems for places that need parts that work well. As machines and computers advance, lattice structures will continue to help us make new things. This will lead to better parts for airplanes, medical devices, automobiles, and electrical systems.